About Our Project
This project was completed with four Masters students as part of an Erasmus exchange hosted by the University of Oviedo, Spain. We were based in the Gijon campus of the university and all of our work was carried out here. Two students from the host university also helped with areas of this project, Miguel Herrero Alvarez of the mechanical engineering department, and Alba Abad Sánchez of the electrical engineering department.
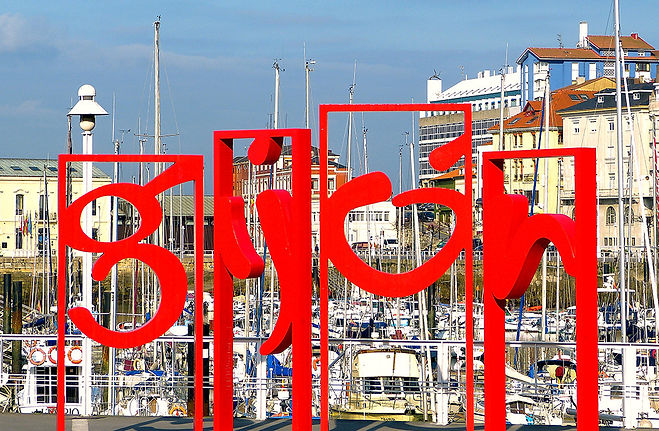
Gijón
Gijón is the largest city in the autonomous community of Asturias, on the North Atlantic coast of Spain. It is home to Escuela Politécnica de Ingeniería de Gijón(EPI), the engineering school of Universidad de Oviedo, as well as a large engineering centre for Duro Felguera, the company that proposed this project, with a department in Gijón focused on warehouse logistics systems. The group lived in the city centre of Gijón during the semester abroad.
Life Studying Abroad
Living in the city centre of Gijón meant there was always a lot to do in our spare time. All members of the team were also lucky in finding accommodation very close to the main beach, Playa de San Lorenzo. This meant there were many sports easily accessible when weather permitted including volleyball, ultimate Frisbee and football.
We were also lucky by being there during ‘Asturias Day’, a large celebration of the autonomous community in the part of Spain where we were staying. The Gijón International Film Festival also took place during our time there and some members of the group took advantage of this.
Our location also allowed for much travelling to take place and group members visited such places as: León, Valencia, Barcelona, San Sebastian, Salamanca, Porto and Lisbon. This was made even more enjoyable by the fact there was a strong Erasmus community in the city many of whom we travelled with. Thursdays were typically designated as tapas night, which were well organised by the a network for Erasmus students, run by local Spanish students. They were a good opportunity to get together with everyone studying on Erasmus in the city.
Our Project
The team was assigned a project concerning the full design and manufacture of a prototype automated palletizing machine which is capable of fully loading a standard scale Europallet with boxes in varying orientations from layer to layer. This proved to involve many challenges to be overcome and as such was broken up into smaller constituent systems all necessary to achieve our goal. These parts were: A hopper system used to feed the boxes at appropriate intervals; a conveyor belt used to transport the boxes further down the line; a pushing mechanism used to push the boxes onto the pallet at the appropriate time (ie upon the completion of each row); a loading system used to collect all the boxes in each layer in position before laying them onto the pallet; and a lifting mechanism used to raise the pallet to an appropriate starting height, and then lower in adequate increments for each subsequent layer.
For this project the team was allocated a budget of up to 500€ to buy any parts unavailable in the lab, however great emphasis was given to recycling parts from previous projects and manufacturing parts using whatever materials were available in the lab. This added an interesting challenge to the project by presenting particular design constraints.
We were assigned a supervisor to help us along with this project, Dr José Manuel Sierra Velasco, who aided us from the initial briefing all the way through to the building process. José also helped greatly in securing us a room to work quietly in and by providing a key to the lab our machine was being built in, which proved to be of great help. We were also put in touch with the lab technician, Yago, who was of great help in manufacturing some of the parts using techniques the members of the group were less proficient in, and in helping provide a lot of materials needed. The lab we were assigned to work in had a pillar drill, angle grinder, vice and welding equipment (used by Yago) which were particularly convenient during the build.
Our Team

My primary role within the project was the design and construction of the conveyor belt. This project gave me an exposure to Solidworks, and was my first truly practical project over my University career which I thoroughly enjoyed. Outside of University life, I loved learning Spanish, travelling around Spain and learning to surf.

I was working primarily on the design of the hopper mechanism, as well as engineering calculations, simulation and management methodology for the project. As part of the work I learned to use Solidworks and WorkingModel software, and I learned about detailed mechanism design, an area that I didn’t have previous experience of. I enjoyed living in a new city and meeting people from other places. I also enjoyed working closely with our supervisor and learning about his areas of work.

My main role was the design and build of the pusher mechanism. I had done quite a bit of CAD modelling before the project, but this was my first experience of a manual build of a part I had designed and I enjoyed being involved in the practical build. I was also responsible for keeping minutes of all the meetings and important updates on the project. Out with the project, living next to the beach was great and I enjoyed taking surf lessons and spending weekends travelling around Spain.
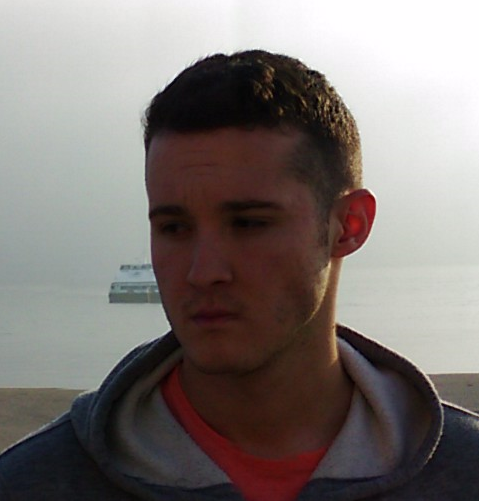
My main role was the design and build of the lifting mechanism. Whilst being new to Solidworks I did have some degree of experience using CAD and this proved invaluable. Experiencing working hands-on in the lab was interesting and engaging for me. Away from the lab I took advantage of the local surfing culture and played some amount of futsal including with the academic staff! This was also a great opportunity to travel more and I visited many places during my time in Gijon.